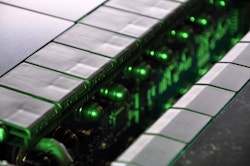
Batteries
Are you interested? Contact us for a personalised quote
Batteries are made up of accumulators. Batteries have the particularity of storing energy and being able to be recharged. They comprise cells, each equipped with a positive electrode (the cathode), a negative electrode (the anode), a separator and an electrolyte which delivers electrical energy by changing state. Depending on the chemical components and the materials used for these elements, the properties of the battery are different and have an impact on the quantity of energy stored and delivered, the power supplied as well as the number of possible charge and discharge cycles. Battery manufacturers are constantly looking for more economical, denser, lighter and more powerful electrochemical systems.
Batteries content
Looking back into history
In 1786, biologist Luigi Galvani dissected a frog. Every time Galvani's steel scalpel touched a copper hook, which held the frog's leg in place, it contracted. Galvani thought that this energy came from the animal and therefore called it "animal electricity". Alessandro Volta, apartner of Galvani, did not agree with this idea. He was convinced that the electricity had been generated by the two different metals in a moist medium. Experiments then confirmed this idea and, in 1797, Volta designed the first battery: the voltaic pile. It was made up of 49 pairs of copper and zinc disks, arranged alternately, separated by a cloth soaked in salt water. But in a voltaic cell, electricity is generated by a chemical reaction and when it runs out, the cell cannot be recharged.
In 1899, Waldmar Jungner, a Swede, invented the nickel-cadmium battery. In 1947, Neumann succeeded in completely sealing the accumulator. These advances led to the modern sealed nickel-cadmium battery.
The first primary lithium batteries, without recharge, appeared in the early 1970s. Attempts to develop rechargeable lithium batteries followed in the 1980s but failed due to safety concerns. Because lithium in metallic form is naturally very unstable, particularly during charging, research then turned to non-metallic lithium batteries using lithium ions. Although slightly lower in energy density than its metallic lithium counterpart, Lithium-ion (Li-ion) is not dangerous if precautions are taken when charging and discharging.
The vast majority of current electric or hybrid vehicles are equipped with lithium-ion batteries. This type of battery is also found in telephones, laptops and many other devices. Its inventors, Stanley Whittingham, John Goodenough and Akira Yoshino, were awarded the 2019 Nobel Prize in Chemistry. In the 1970s, in the midst of the oil crisis, Whittingham demonstrated the advantage of lithium over other metals used until then (copper, platinum, nickel, etc.) to store more energy with reduced bulk and weight while offering a longer service life. He then created the first lithium battery thanks to the financial contribution from oil company Exxon. But the oil crisis being over and the high production costs that industrialization of batteries would generate led Exxon to stop their development.
In 1980, the American Goodenough undertook to replace the metal sulphide of the cathode with cobalt oxide, at the same time doubling the performance of the battery when increasing in voltage. But the rapid release of electrons and the agglomeration of lithium ions at the end of the electrodes, with a risk of contact and therefore of short circuit, required stabilization. This issue was sorted in 1985 thanks to the Japanese Yoshino, who used petroleum coke for the anode, which led to the marketing of the first li-ion battery by Sony Corporation in 1991.

Why Lithium-ion batteries dominate the market?
Today, Li-ion battery technology allows the highest level of energy density, up to 5 times more than Nickel batteries. Performances such as fast charging up to 80% of their capacity, or the temperature operating window (-50°C to 125°C) and their uses can be refined thanks to the wide choice of cell designs and chemistries. In addition, Li-ion batteries have other advantages such as very low self-discharge, very long life and great cycling performance, typically thousands of charge/discharge cycles.
What the main chemistries of Lithium-ion batteries?
There are different types of Lithium batteries, depending on the chemistries used in combination. It's all about compromise. In the automotive industry, Tesla uses NCA and all the others use NMC (Nickel Manganese Cobalt). In other industries, and especially for boats, we find LTO (Lithium-Titanate, developed by Toshiba) and LFP (Lithium-Iron-Phosphate) for their safety and their lifespan. LFP is more energy efficient than LTO. LTO is made for high cycling, fast charging, but little autonomy — it is expensive and heavy. The LFP on electric or hybrid boats is a good solution to combine safety, performance and lifespan; Less dense than the Lithium NMC technology used in cars but much less prone to thermal runaways leading to battery fires that are impossible to extinguish, LFP technology is also found in medical and solar applications.
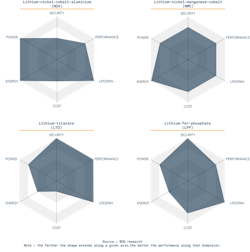
What are other current lithium-ion battery chemistries?
Lithium-polymer (LiPo)
This electrochemistry is very powerful in discharge and has no memory effect, but its lifespan remains short compared to its price. These batteries are found in model aircraft applications and in connected devices.
Lithium-nickel-cobalt-aluminum (NCA)
Dense in terms of energy and power, the NCA is more economical than the NMC. Nevertheless, it is almost as sensitive as the NMC, which limits its use. It is widely used for applications in electric mobility or high power, such as golf vehicles for example.
Lithium Manganese (LMO)
Here the cobalt is replaced by manganese, thus making this technology more durable and more economical. However, its lifespan is short with an average of between 300 and 700 cycles.
What are the new developments?
New electrochemical technologies have been developed in recent years:
- Lithium-sulfur: Still under development, these batteries are light, economical and very capacitive. The only problem: their short lifespan.
- Lithium-metal-polymer (LMP): Easier to recycle, LMP nevertheless has a very short lifespan for an average capacity.
- Lithium-air: Dense in energy, this technology is still under development because it is very corrosive.
- Lithium-cobalt-oxide (LCO): Composed of cobalt, this technology has a very high cost and can be very dangerous. Nevertheless, it remains significantly capacitive.
The manufacturing of batteries often raises questions about their recyclability, the rarity of metals... what's the reality?
Most materials are not that rare, not that polluting either, especially for LFP chemistry. Lithium, iron phosphate, aluminum, copper. No Nickel, no Cobalt, no Manganese, no Lead, no Cadmium, no heavy metals, no glues, no coolant, no resins...
The recycling channel is set up. Today, it exists at pre-industrial levels, but the cost of recycling is already very low (1€/kg) and will continue to fall as volumes increase. Recycling recovers metals for reuse.
Some batteries can be completely dismantled, and their recycling makes it possible to sort the components upstream to either reuse them or reduce the cost of treatment. If we take as an example an LFP battery such as those developed by EVE System (partner of EODev), it has a carbon footprint of less than three tons of CO₂ over its entire Life Cycle Assessment. The equivalent of approximately 10,000 kms traveled with a Diesel car or truck which would consume 10L per 100 kms. Which, at an average speed of 100 km/h on the motorway, corresponds to a hundred hours of use, compared to several hundred or even thousands of cycles for a Li-ion battery.
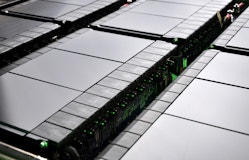
How are batteries certified for marine use?
The maritime sector imposes, depending on the size of the boats, to comply with the rules of marine certification of the installations. This goes through "type approvals" on the components, and more or less extensive design reviews by the certifying bodies. This "type certification" concerns all the safety components of the vessel, such as motors, shafts, propellers, gearboxes, variators, batteries, gas controls, circuit breakers, cables, etc. The marine certification of batteries consists of meeting specific environmental tests (vibration, damp heat, dry heat), functional tests, standardized performance tests (IEC 62619 and IEC62620). Compared to conventional industrial standards, the level of vibration resistance is higher, and the damp heat test is drastic.
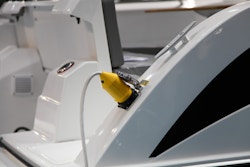